Maintaining a vessel available for production and operation is a great challenge if one considers safety, costs, operation, technical requirements, and human constraints, all within harsh natural environments.
Bourbon Tech Solutions proposes a two-fold solution:
- Planned maintenance services to strictly comply with safety, class, regulations, standards and manufacturer recommendations, and manage the maintenance plan with high standards.
- Risk-based maintenance services to optimize the maintenance, costs, risks and performance, with customized solutions and expertise.
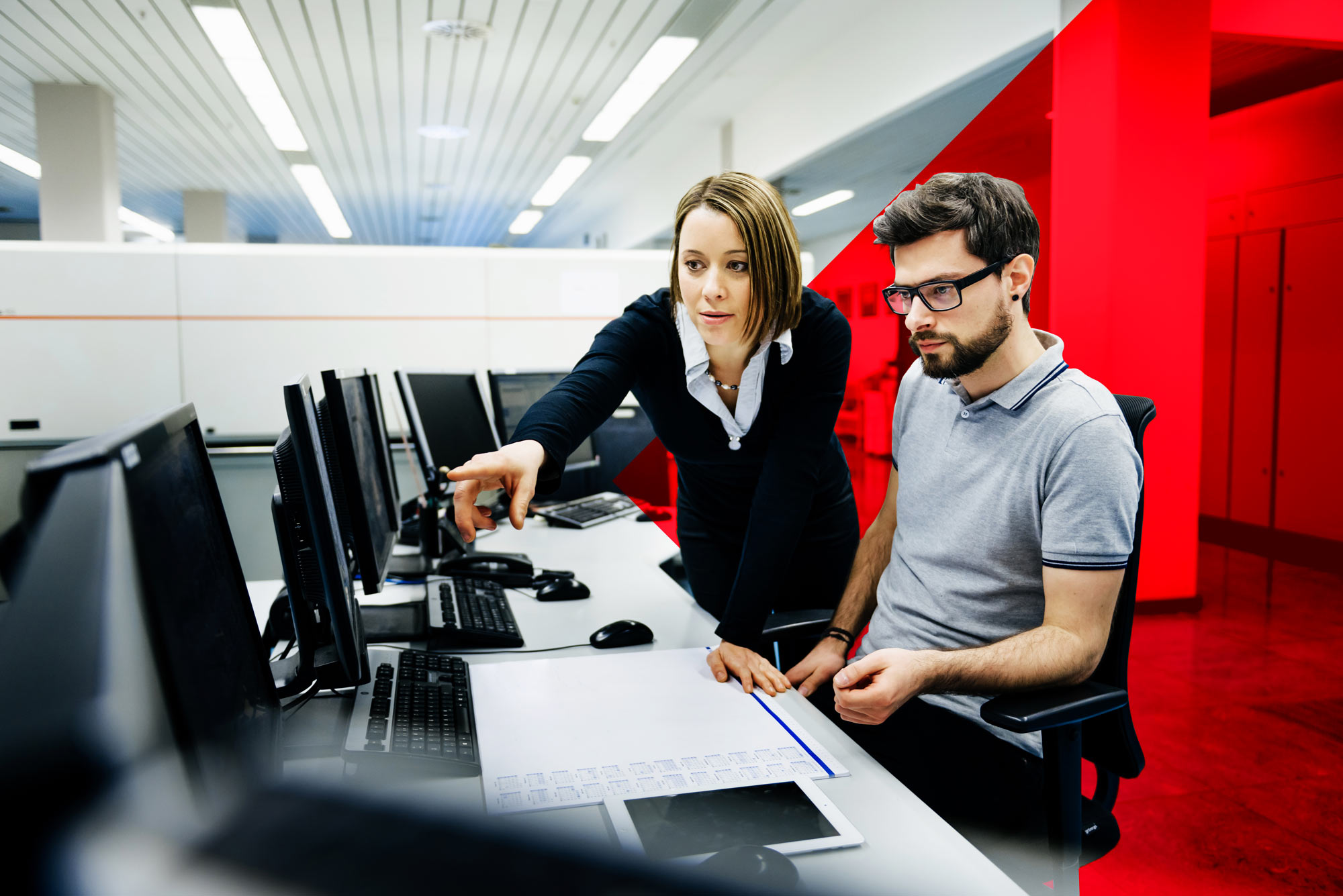
Planned Maintenance Services
PMS SPECIFICATION AND DEPLOYMENT
A Planned Maintenance System (PMS) is a document that consolidates all equipment-related preventive maintenance tasks with the objective of ensuring the maximum reliability of said equipment and its longest safe life span. A PMS contains the equipment maintenance planning, procedures and required resources to ensure its sustainability over time.
The development of a PMS relies on several factors:
PLANNED MAINTENANCE SYSTEM DEPLOYMENT
A Planned Maintenance System (PMS) is a piece of software dedicated to the application of PMS through a comprehensive, user-friendly interface. It usually offers various services such as :
-Preventive maintenance plan
-Defect notification and corrective maintenance report
-Spare parts for each equipment
-Inventory
-Purchase module
All PMS software providers Bourbon Tech Solution works with are class approved.
Upon approval of PMS, we ensure the deployment and data population of your PMS database starts with the support of PMS data officers and managers until complete uploading of the PMS. Methodology and quality checks are key there as quality of data contributes to the level of efficiency of the PMS.
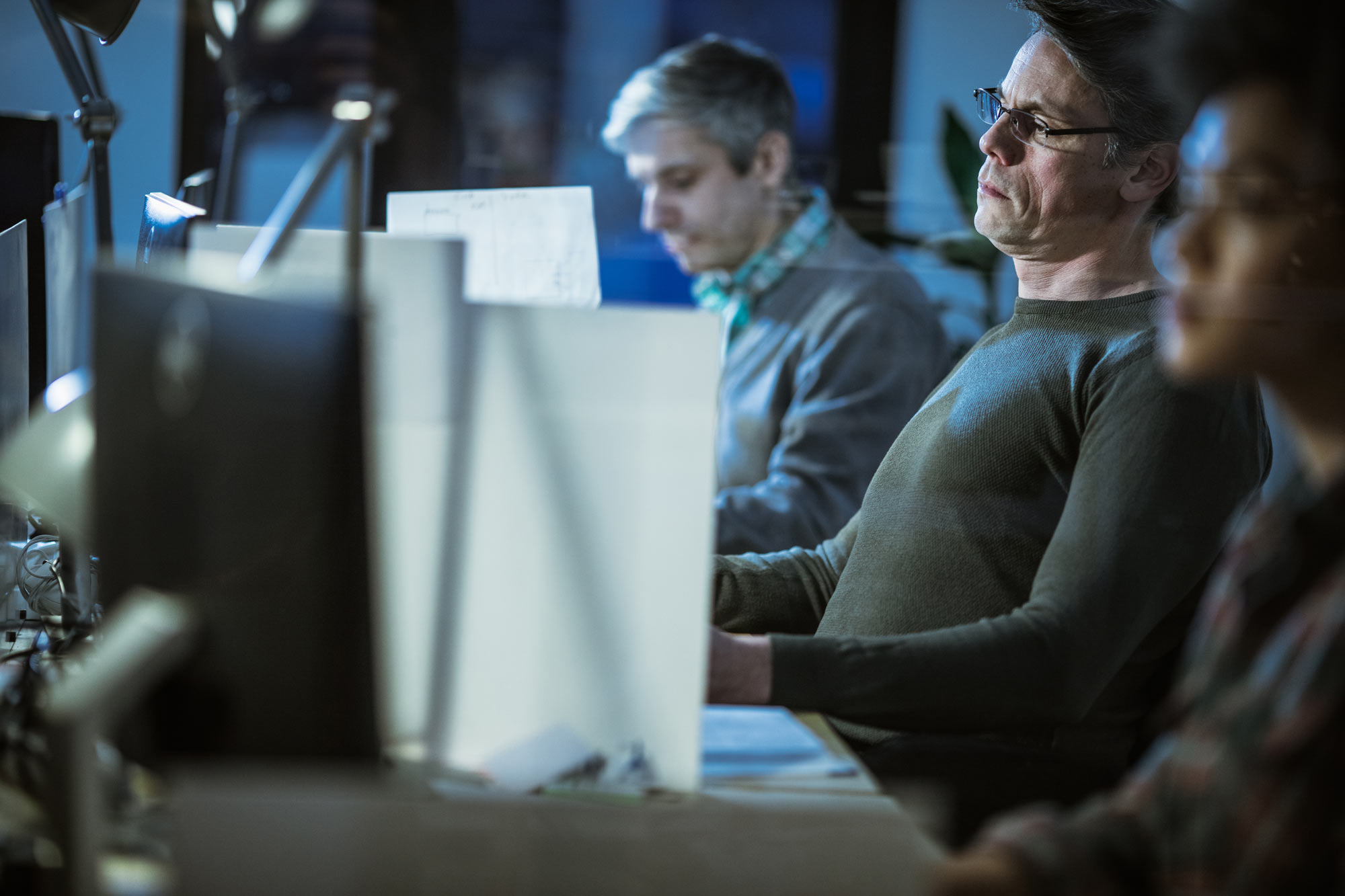
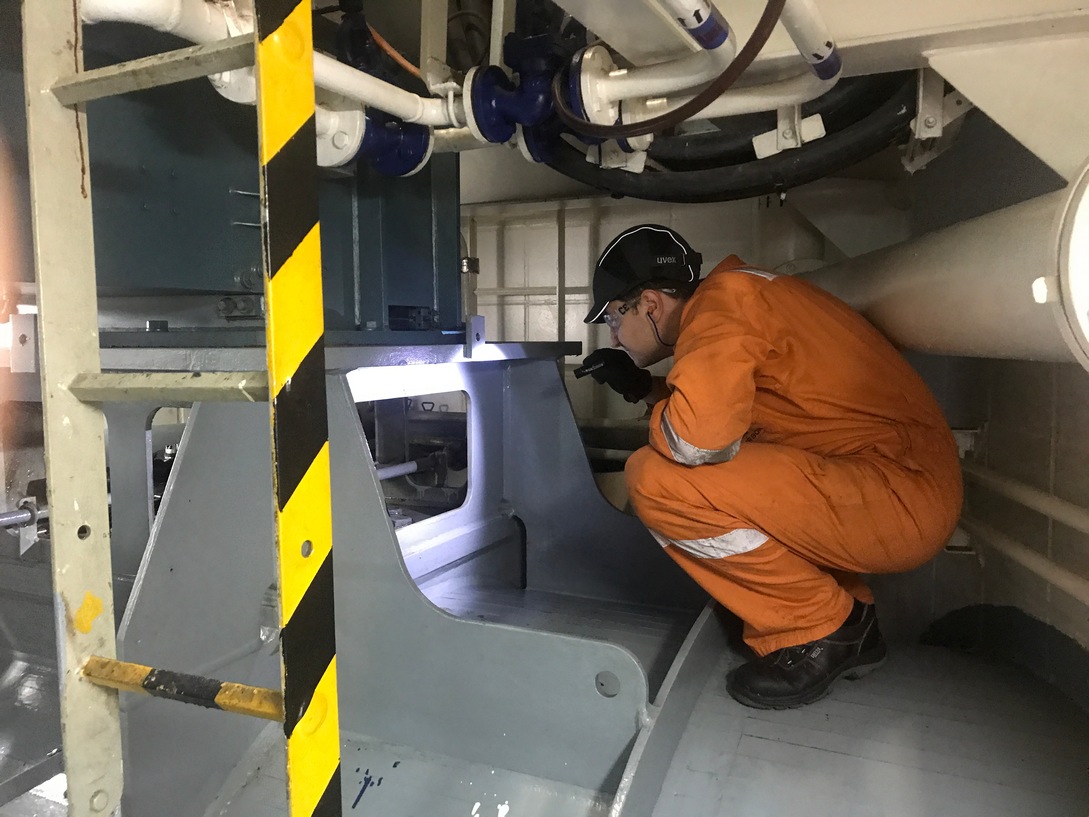
DATA COLLECTION
Proper on-site data collection is essential to the quality of the PMS database. Indeed, a great part of the efficiency results from accurate, complete data. Our experts follow rigorous methodology and have great experience in data collection, as we ran through the process hundreds times for large Bourbon fleet vessels. It can take five to 10 days for an experienced officer to complete, from scratch, a thorough data collection on a PSV-type vessel, covering approximately 2,500 components.
PMS DESIGN
With years of experience, our PMS expert team will develop your PMS with:
PMS MANAGEMENT
Planned Maintenance System (PMS) is a continuous improvement process based on the consolidation and analysis of preventive and corrective maintenance carried out by crew or yard. Our expert team ensure the supervision of your PMS to ensure crew report quality and provides failure analysis, recommendation or alerts. Evolution of PMS and preventive maintenance is made to further improve reliability and technical availability of your vessel.
PMS ADMINISTRATION
Our PMS expert team ensures regular watch on your PMS to populate spare part (create new or follow up on maker new references), to modify preventive maintenance plan as per PMS directives, to improve job description or to follow up user experience and keep it at higher level
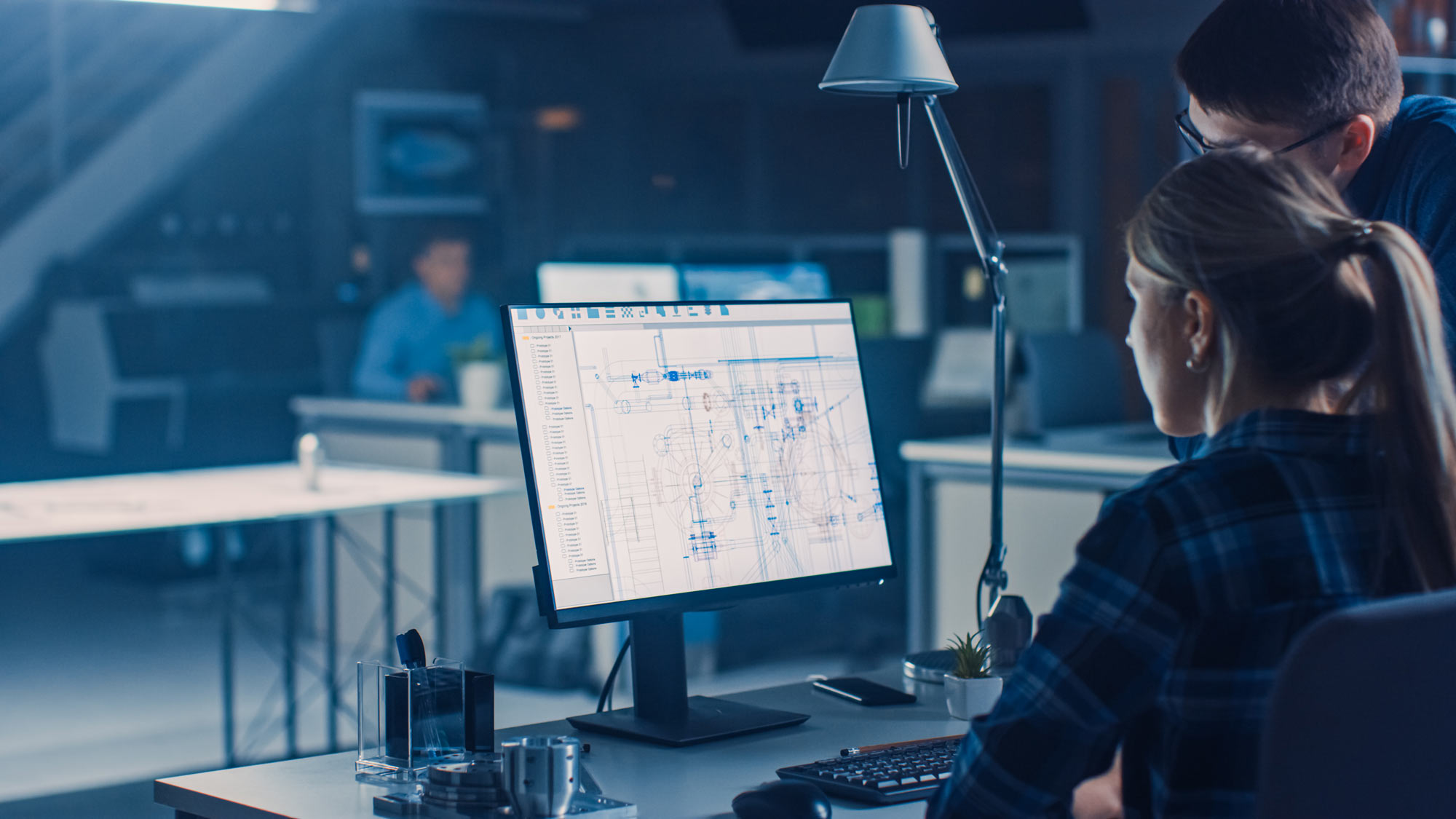
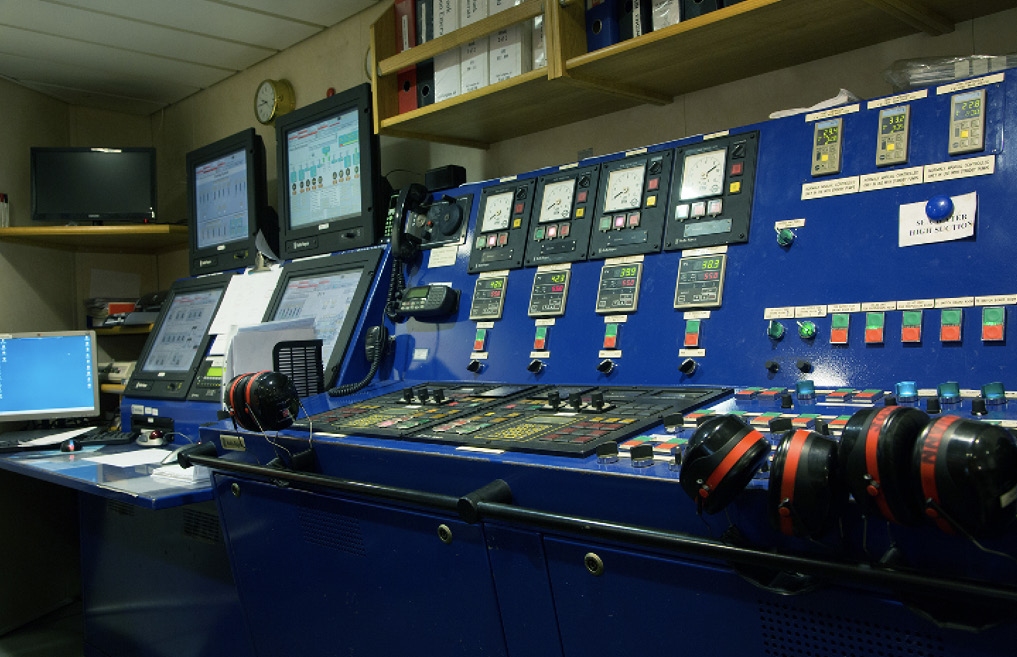
Risk-Based maintenance services
CONDITION-BASED MONITORING (CBM)
CBM is a maintenance strategy that monitors the actual condition of an asset in order to decide what maintenance needs to be done. CBM dictates that maintenance should only be performed when certain indicators show signs of decreasing performance or upcoming failure.
Through our partnership with SKF, we offer our customers deployment of vibration analysis solutions as a part of a condition-based monitoring strategy. For example, one of the benefits this solution may bring for a typical OSV – is avoiding cash-out by postponing bearing replacement on propulsion motors for coming dry dock.
RELIABILITY-CENTERED MAINTENANCE
Reliability-Centered Maintenance (RCM) is a methodology to optimize the maintenance plan and to ensure maintenance tasks are performed in an efficient, cost-effective, reliable and safe manner. RCM methodology is well known in the aeronautical and energy industries, and our experts have been trained and certified to be able to implement it on vessels. We have already implemented Reliability-Centered Maintenance in more than 50 of OSV maintenance plans, with results up to 25-30% of savings.
PREDICTIVE MAINTENANCE
We can offer predictive maintenance services with data analysis tools and techniques to detect and anticipate anomalies in operation and possible defects in equipment and processes before failure occurs. Our methodology consists in collecting, treating and analyzing data before systems generate alerts.
We can offer a set of solutions to implement a predictive maintenance methodology in accordance with clients’ needs.